社内コンペ日記#2 Ceiling Light スタディ編
コンペの目的
今日は前回の記事で紹介した社内コンペ、天井照明の実製作に入る前のスタディ段階を紹介していこうと思います。
と、その前に、このコンペの目的についてまだ説明していなかったと思うので、説明しておくと
- 日常的に使っているソフトウェアやそのノウハウをいつもとは違った形で使ってみる
- 通常の業務では使うタイミングがないが試してみたいツール、手法を使ってみる
- たまにはデザインをして頭を柔らかくしてみよう
というような狙いがありました。シンテグレートの日常の業務ではデザインをすることはありません。しかし日常的に3Dに慣れ親しんでいる中で、試してみたいソフトウェアや、このテクニックを違う使い方で使ったら面白そう、と思うような場面にも出くわすので、そういったものを試す機会としてやりました。この天井照明について言えば、
- 複雑な形状をメッシュベースでスタディ
- 3Dプリントを大きなプロダクトサイズで展開する際のやり方
を試したい、というところが発端です。
3つのポイント
ではここから本題にいきましょう。実際製作するにあたって大きく三つのポイントがあります。まず、
デザイン
実製作段階では理想をそのまま実現することは不可能です。様々な条件に対して変更、調整をしていく必要があります。その際に意匠上、守りたい箇所と諦める箇所の線引きをしておくことが大事です。2つ目は
技術的、材料的に可能か
これは言葉通り、こちらの作りたいものが技術的、材料的に可能かというものです。最後に
予算
これが一番大事ですね。通常、これが物事の8割を決めてしまうと言ってもよいと思います。予算と作りたいものの落としどころを見つけることが、ここでも重要になってきます。よく設計でもVE案(Value Engineering(バリューエンジニアリング)といって、性能や価値を下げずにコストを抑えること)で毎回苦しむのが常であるように、ここでも、どうコストを上げずに当初のイメージをキープするかでスタディを重ねました。
検討案の変遷
これが検討案の変遷です。順を追って簡単に紹介していきます。
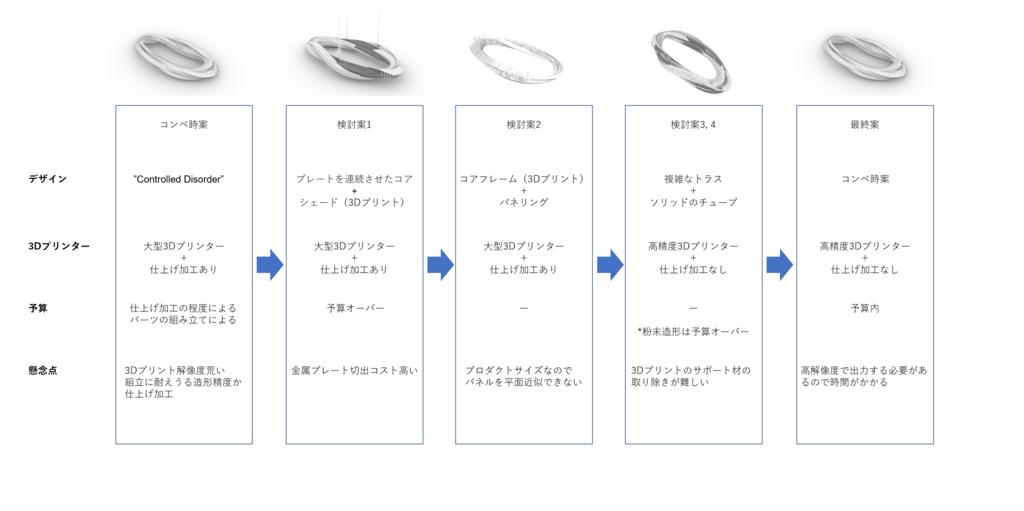
今回はコンペ時案のイメージがあったものの、様々なパターンを検討してみました。3Dプリントだけでなく他素材を組み合わせたものもフラッシュアイデア的にやりました。
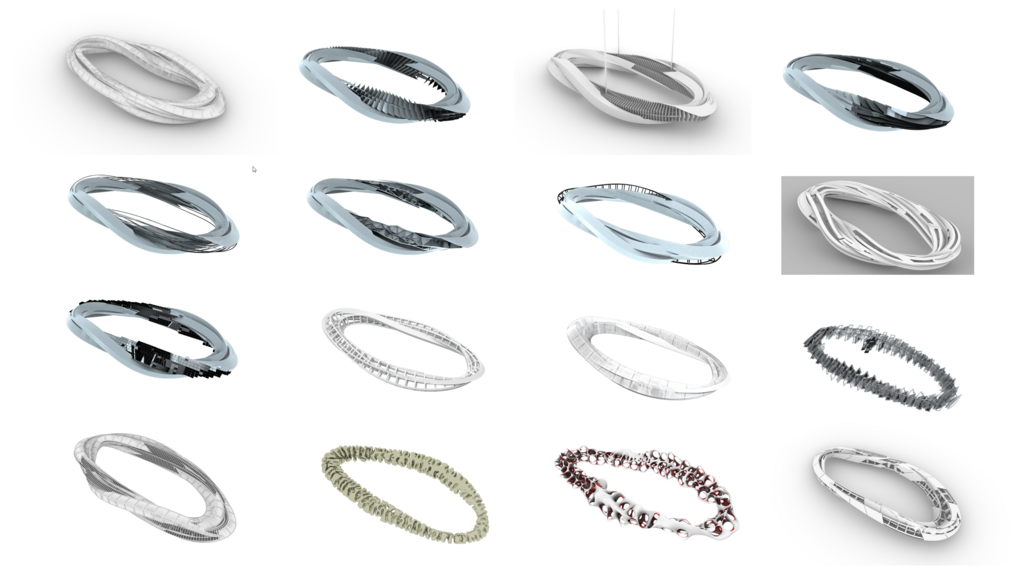
案1 “プレートを連続させたコア + シェード”
これは断面形状をプレートで連続させたコアを作り、シェードとなる部分に3Dプリントを用いたものです。シェードの形状はチューブの重なった箇所を部分的に消してコアのプレートが見えるようになっており、これらプレートは照明の反射板の役割も果たします。しかしこれは金属プレートの切り出しが高くなり、予算オーバーでした。
- 3Dプリンター: Massivit (大型3Dプリンター)+ 仕上げ加工あり
- 予算:オーバー
- 懸念事項:金属プレートの切り出しコストが高い
- 結論:却下
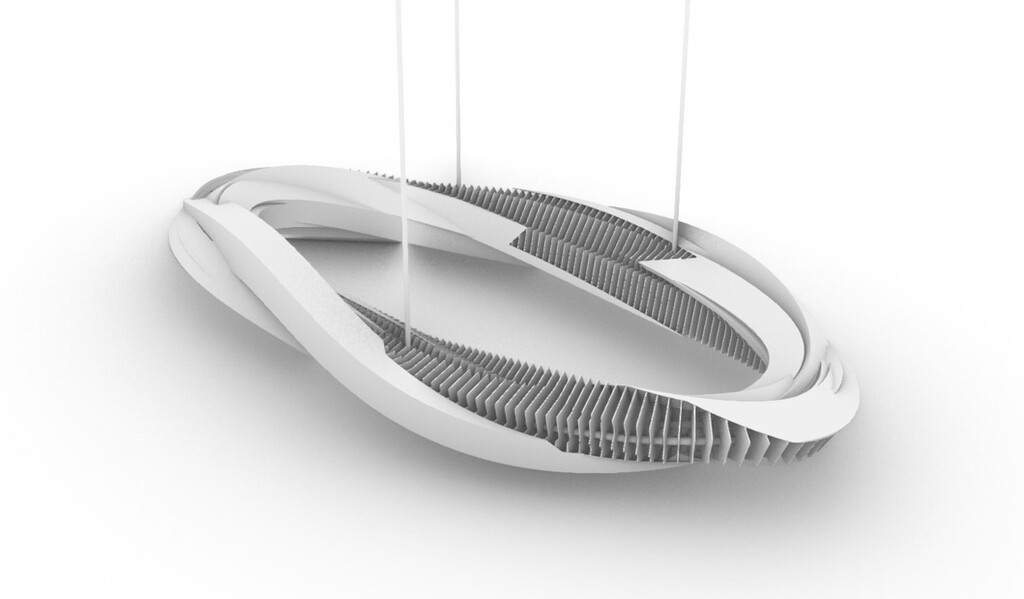
案2 “3Dプリントストラクチャー + パネリング”
これは3Dプリントでコアとなるフレームを作り、その外周のサーフェスを平面に近い形状まで近似しパネリングをする案です。シンテグレートの普段の業務から着想を得た案ですが、建築スケールではパネルとパネルのギャップを目地で吸収できますが、このプロダクトレベルのスケールではそれが難しいことが懸念でした。
- 3Dプリンター: コアストラクチャー/ Massivit (大型3Dプリンター)+ パネル/ 板材
- 予算: ー
- 懸念事項:サイズが小さく、パネルを平面近似できない
- 結論:却下
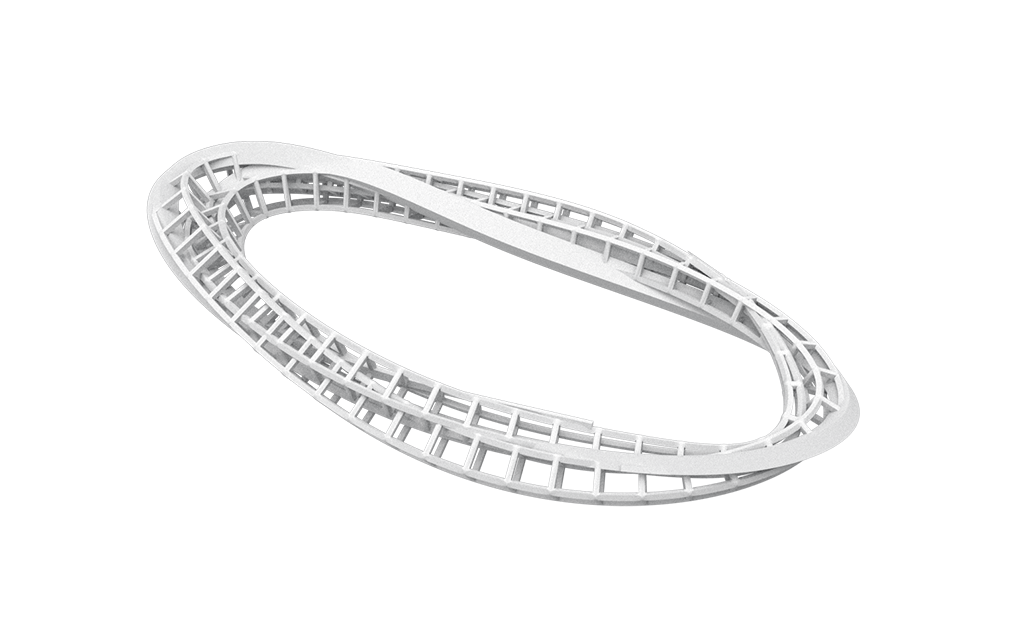
案3 “複雑なトラス + ソリッドのチューブ”
そこで頭を切り替えて、やはり3Dプリントならではの形状をつくるという方向にシフトして検討していった案がこちらです。入り組んだトラス状の部分とソリッドのチューブが絡み合っている形状です。このソリッド状のチューブの内部にLEDを仕込む想定です。これで3Dプリントのテストサンプルを作成しました。
- 3Dプリンター: Raise3D(高精度3Dプリンター)+ 仕上げ加工なし
- 予算:ー
- 懸念事項:形が入り組み過ぎて、プリント時に必要なサポート材の取り除きが不可能
- 結論:却下
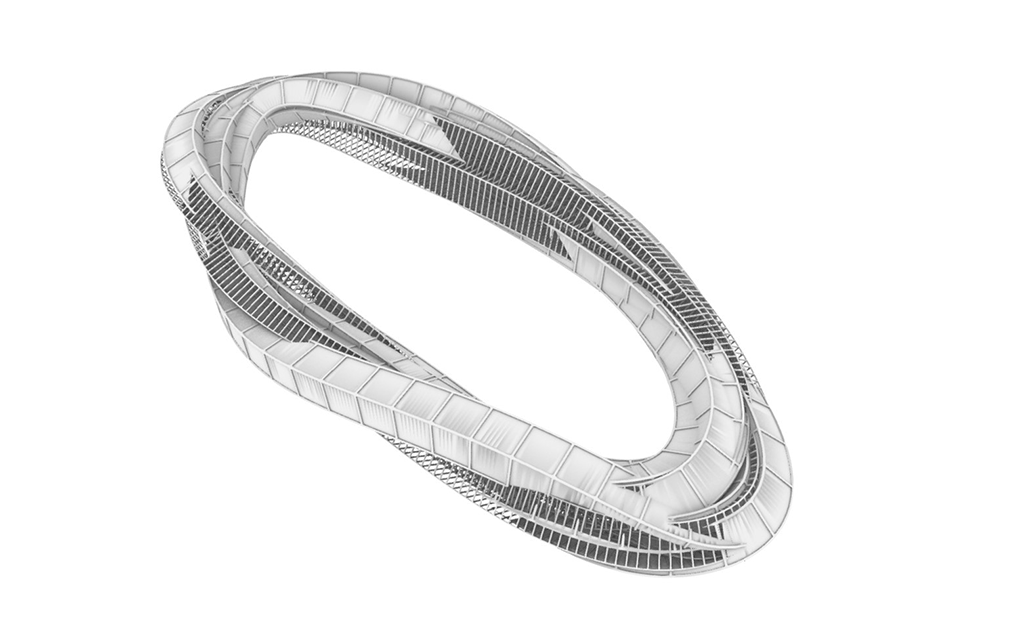
今回、3Dプリントは穴織カーボン株式会社さんに入ってもらい、試作品含めて全面的にサポートしてもらっています。そして、下の写真が作ってもらったテストモデルです。本来のトラス状の部分よりも、それをプリントするためのサポート材の存在感がすごいですね。実際、この出力されたテストモデルのサポート材をきれいに取り除くのは相当難しかったので、サポートの充填率を下げて、極力簡単にサポート材を取れるようなバージョンも検討しました。しかし状況は写真のものとあまり変わらなかったので、水溶性サポート(水で溶けるサポート材)もトライしました。しかし、これは造形自体が安定せず、うまくいきませんでした。最終的に、サポート材が必要な3Dプリントでこの形状を作るのは現実的ではないと判断しました。
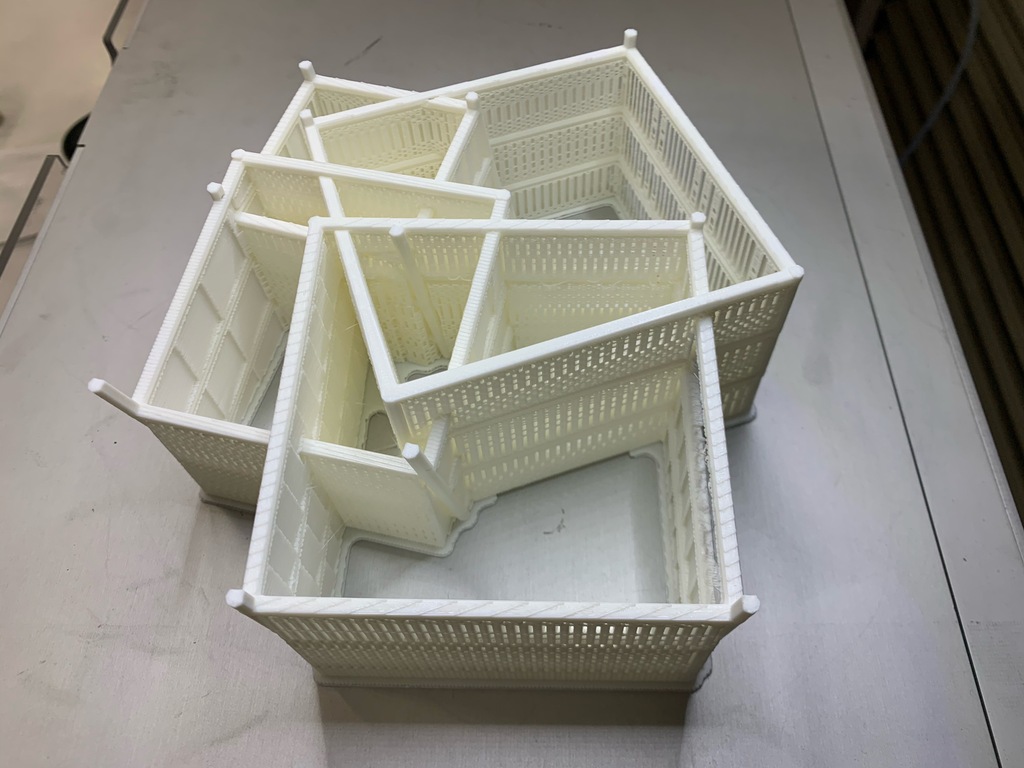
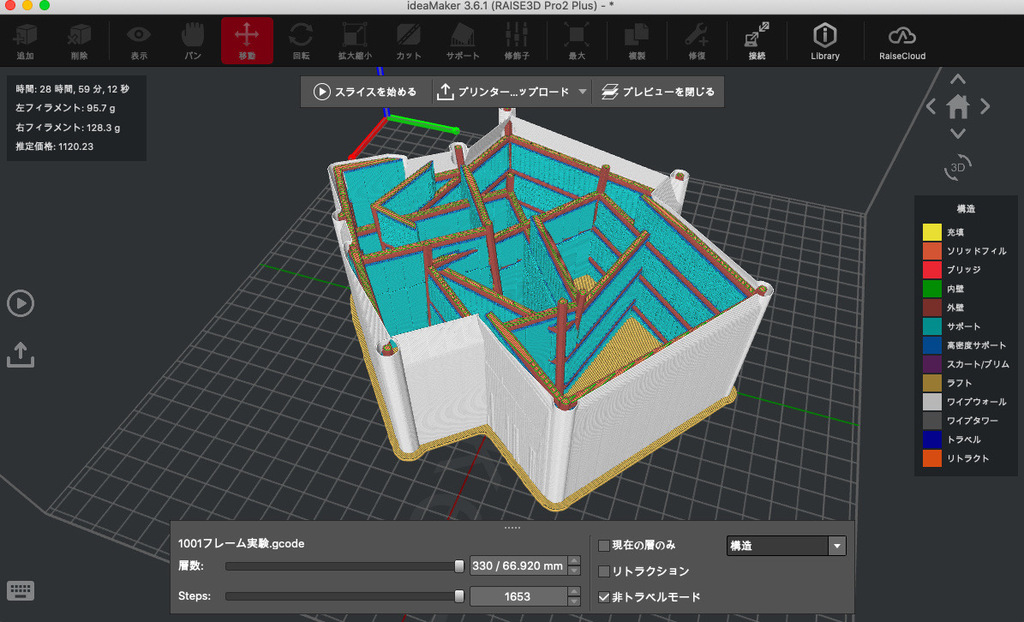
案4 “案3の形状で3Dプリントマテリアル変更”
そこでサポート材が必要ない、粉末造形を検討しました。しかし大幅に予算がオーバーしたので、長手1,500mmにしてサイズを3/4にしてみましたが、依然2倍以上予算がオーバーしていたので却下しました。
- 3Dプリンター: 粉末造形
- 予算:オーバー
- 懸念事項:当初サイズ(長手2m)からサイズダウン(長手1.5m)するも予算オーバー+組立時の強度不安
- 結論:却下
最終案 “初期案形状で3Dプリントマテリアル再検討”
これまでの過程の中で、このスケールのものを3Dプリントで作る際のポイント、金額感、実際の3Dプリントの出力で可能な解像度などが感覚的にわかってきたので、その落とし所を再考しました。
そこで当初のコンペ案に立ち戻り、これを二種類の3Dプリンターで再度テストサンプルを出しました。一つはアクリル系の素材をUVで固める形式のもの、もう一つがPLAという素材で、こちらが本命です。その2つを見るとプリント機の特徴が如実に出ることになりました。アクリル系で出力したものはチューブから出したような積層が見え、エッジが立つような形状には不向きであることがわかります。一方 PLAのものは積層して出力するものの、一層一層がかなり細かいため、角がたち、形状の再現性は高いことがわかりました。
- 3Dプリンター: Raise3D(高精度3Dプリンター)+ 仕上げ加工なし
- 予算:OK
- 懸念事項:高精度で出力すると3Dプリントの出力にかなり時間がかかる
- 結論:採用
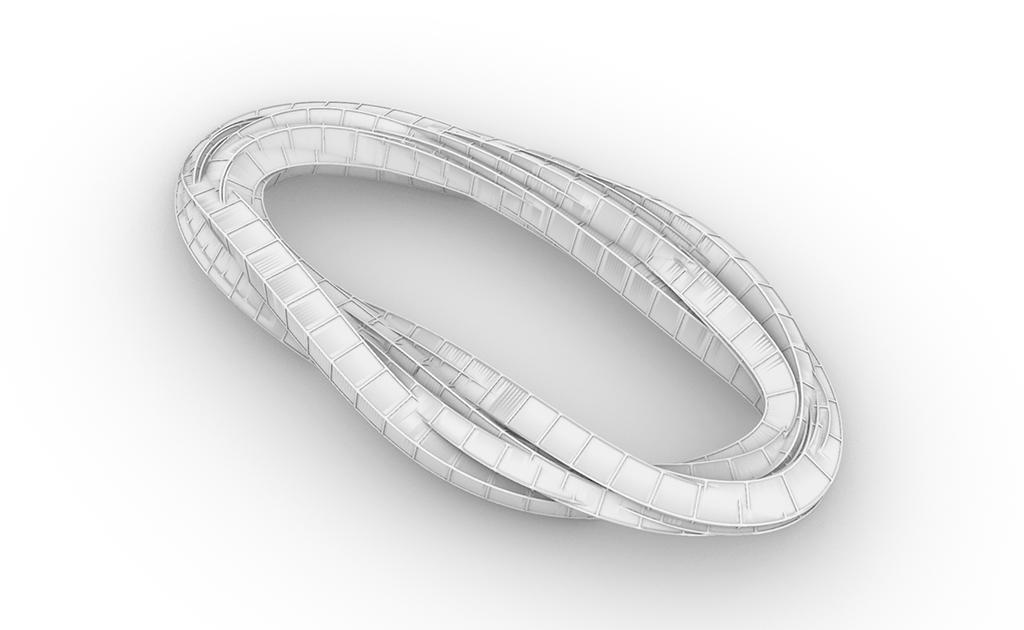
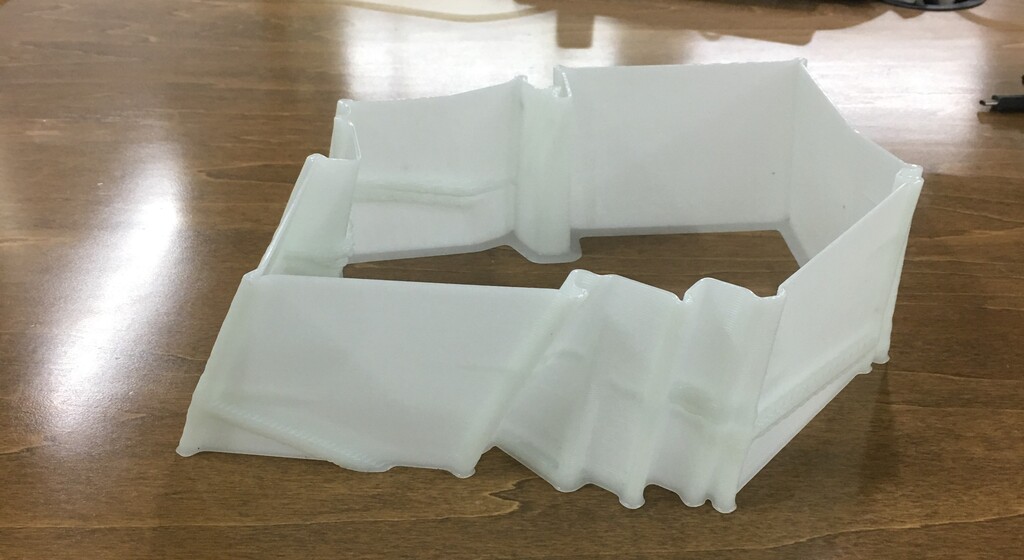
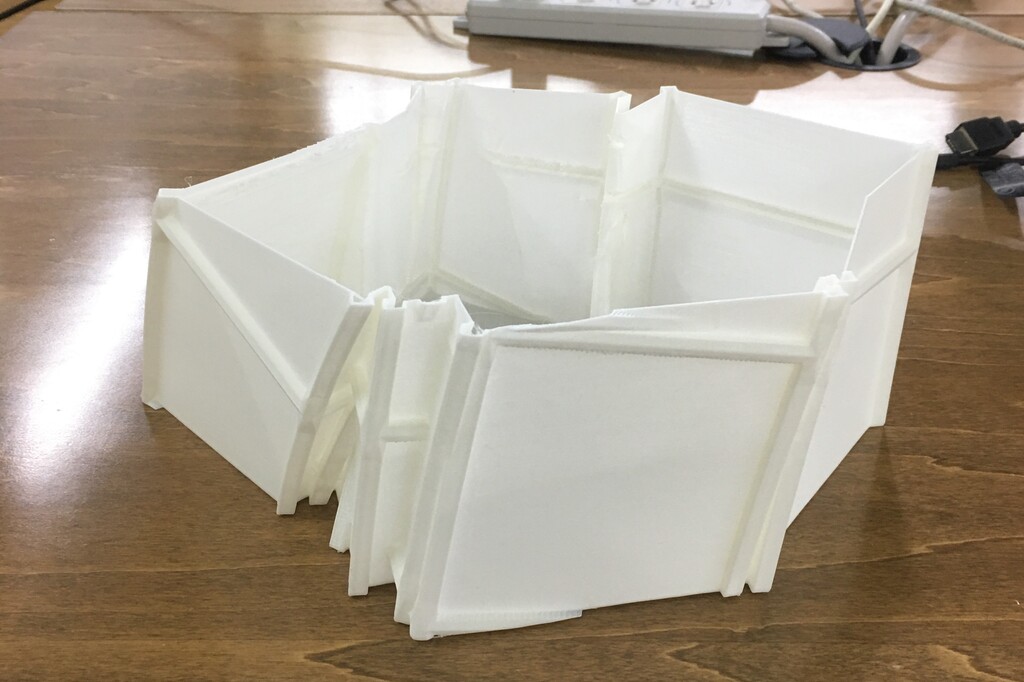
こうして紆余曲折を経て、ようやくデザイン、製作の方針が見えてきました。
これでいきます。
ではまた。次回へ続く。
次回予告
- コンペのコンセプト「Controlled Disorder」
メッシュモデリングツールの可能性- 「コンピュテーショナルデザイン≠最適解、効率化」という話
- ツール由来、ボトムアップのデザインのおもしろさ
Ceiling Light スタディ日記- Ceiling Light 製作日記①
- Ceiling Light 製作日記②
パーツ毎に出力したモデルたちです ↓
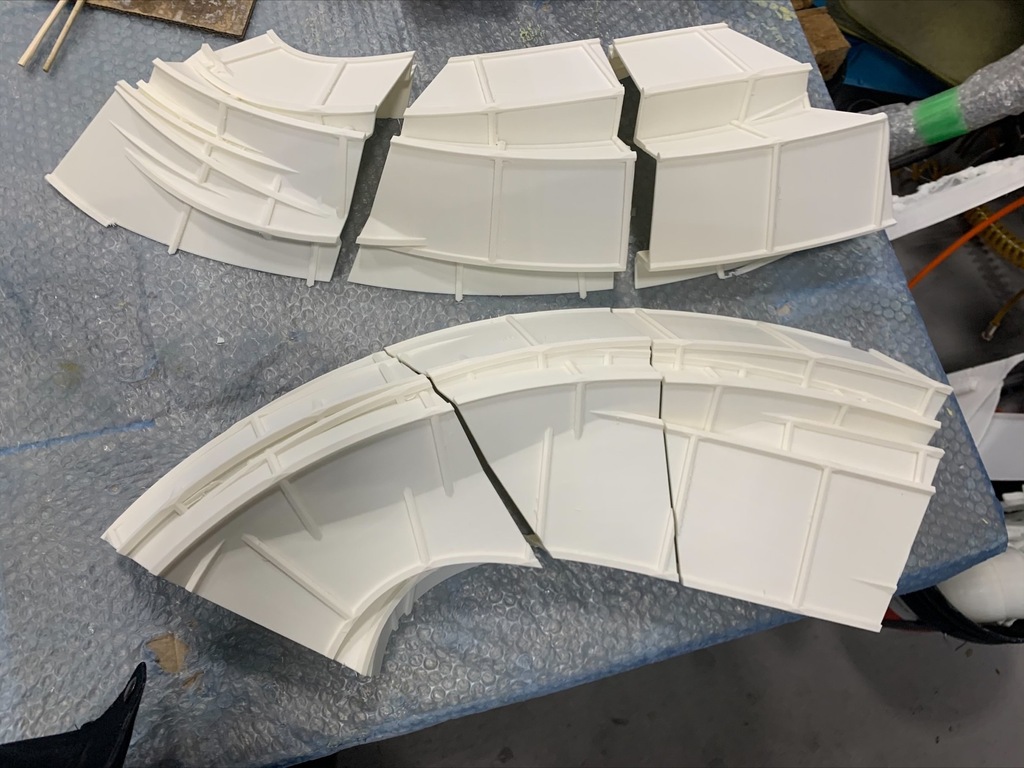